Lograr emisiones de NOx ultrabajas sin EFGR en aplicaciones de adaptación de quemadores
CATEGORÍAS:
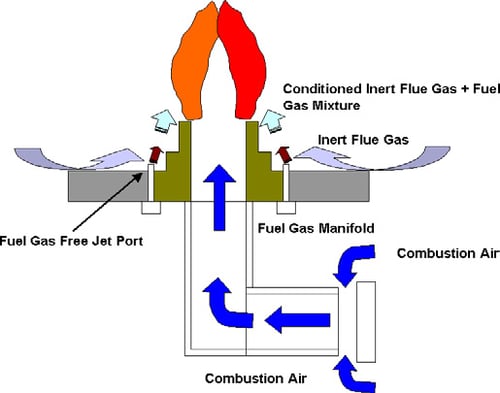
La retroadaptación de quemadores de bajo NOx en aplicaciones existentes puede ser una solución económica para conseguir niveles bajos de emisiones de NOx en equipos de combustión existentes. Normalmente, los quemadores de bajo NOx requieren la recirculación externa de los gases de combustión (EFGR) o la reducción catalítica selectiva (SCR) para conseguir unas emisiones de NOx de 9 ppmv y 50 ppmv de CO o inferiores. El diseño de un quemador de bajo NOx que se adapte a un recorte de quemador existente y que funcione correctamente dentro de las limitaciones de longitud de combustión y cumpla los objetivos de emisiones sin EFGR ha sido un reto para la industria. La empresa Dow Chemical Company de Pittsburg, California, se enfrentó a este reto cuando su horno Dowtherm® Heater tuvo que funcionar con menos de 9 ppmmv de NOx y 50 ppmv de emisiones de CO. Zeeco suministró a Dow un quemador patentado GLSF Free-Jet Burner retrofit de nueva generación que ofrece una huella mecánica pequeña, un perfil de llama compacto y longitudes de llama más cortas.
La tecnología Zeeco® Next Generation Ultra-Low NOx Free-Jet Burner puede producir emisiones de NOx inferiores a 9 ppmv sin EFGR. El quemador de chorro libre GLSF produce un perfil de llama con una interacción llama-llama muy limitada para las instalaciones de quemadores, al tiempo que consigue longitudes de llama más cortas. El diseño del quemador utiliza la teoría de mezcla "free jet" para maximizar la cantidad de productos internos inertes de la combustión (gas de combustión) mezclados con el gas combustible en la cámara de combustión para producir una mezcla de combustible reacondicionado de gas y gas de combustión. La mezcla resultante arde entonces en el proceso de combustión con una temperatura de llama adiabática más baja y produce emisiones de NOx inherentemente más bajas.
Una preocupación secundaria de la industria para la empresa operadora del usuario final es el coste global de propiedad de los quemadores de NOx ultrabajos de nueva generación. Algunos diseños del mercado han tenido costes de mantenimiento más elevados que los quemadores de emisiones convencionales. La compensación de estos costes es la reducción del uso de costosos sistemas EFGR o SCR para lograr la reducción de NOx deseada.
Zeeco revisará los detalles de ingeniería del quemador Free-Jet utilizado en la aplicación de Dow, cómo el diseño aborda tanto las emisiones como los retos de coste de propiedad, y discutirá los resultados de campo verificados con éxito.
DESCRIPCIÓN DE LA APLICACIÓN
La empresa Dow Chemical Company de Pittsburg, California, se enfrentó a una exigente aplicación de emisiones que requería menos de 9 ppmv de emisiones de NOx para su horno Dowtherm® Heater. El horno requería un único quemador diseñado para alcanzar una liberación máxima de calor de 26 MM Btu/hr (6,55 MM Kcal/hr). El horno era un diseño vertical de tipo cilíndrico, con un serpentín helicoidal de dos pasos. El aire de combustión se suministraba al quemador a temperatura ambiente mediante un sistema de suministro de tiro forzado. En el régimen máximo, el sistema de aire de combustión estaba diseñado para suministrar una presión de aire de 76,2 mm H2O (3" H2O) al quemador. La altura del horno era de 6.584 mm (21,6 pies) con un diámetro del círculo de tubos del horno de 2.896 mm (9,5 pies). El volumen del horno era de aproximadamente 43,3 m3 (1.530 pies3) y estaba diseñado para una temperatura de los gases de combustión de 926,7 °C (1.700 °F). La liberación de calor por superficie de suelo era de aproximadamente 350.945 Btu/pie2 (994.964 Kcal/m2). Las aplicaciones con una liberación de calor por superficie de suelo superior a 350.000 Btu/pie2 suelen considerarse difíciles, ya que la temperatura a la que se produce la mayor parte de la formación térmica de NOx es igual o superior a 1.600 °F.
La modernización de quemadores en aplicaciones en las que las emisiones de NOx deben ser iguales o inferiores a 9 ppmv son proyectos difíciles, ya que suelen requerir el uso de la recirculación externa de gases de combustión (EFGR) o la reducción catalítica selectiva (SCR). Otro problema es conseguir que la huella del quemador de baja emisión de NOx de nueva generación quepa en el recorte del quemador existente. Los patrones o perfiles de llama de los quemadores de baja emisión de NOx de nueva generación que pueden funcionar correctamente dentro de las limitaciones de longitud del quemador también han demostrado ser un reto para la industria. ZeecoEl quemador de chorro libre GLSF se diseñó para utilizar aproximadamente 0,6 lb de vapor/lb de gas combustible inyectado en la corriente de aire para aumentar la reducción de NOx en caso necesario, ya que no estaba previsto utilizar EFGR para esta aplicación. El uso de una pequeña cantidad de vapor era menos costoso que modificar el horno para añadir aproximadamente un 25% a 35% de EFGR, o un sistema SCR normalmente necesario para alcanzar el nivel de emisiones de NOx requerido.
CONCLUSIÓN
The Dow Chemical Company en Pittsburg, California, instaló un único quemador de chorro libre GLSF-16 de Zeeco para cumplir un requisito de emisiones de NOx inferior a 9 ppmv para su horno Dowtherm®. Las aplicaciones que requieren menos de 9 ppmv se consiguen normalmente utilizando la recirculación externa de gases de combustión (EFGR) o la reducción catalítica selectiva (SCR). Sin embargo, para este proyecto de modernización, Zeeco suministró a Dow la tecnología patentada Next Generation Ultra-Low NOx Free-Jet Burner, que presenta una huella mecánica muy pequeña, un perfil de llama compacto y longitudes de llama más cortas. Una vez instalado en el campo, un tercero verificó que las emisiones eran inferiores a 6 ppmv de NOx y a 3 ppmv de CO. La capacidad de cumplir los requisitos de emisiones sin el uso de costosos sistemas de recirculación externa de gases de combustión (EFGR) o de reducción catalítica selectiva (SCR) fue beneficiosa para Dow.
Descargar el documento técnico