Conferencia de productores de etileno de la AIChE 2016 - 11-14 de abril de 2016 - Houston, TX
Introducción
- Las emisiones de NOx ultrabajas, inferiores a 90 mg/Nm3, pueden ser difíciles en el craqueo de etileno
- Los métodos típicos de reducción de NOx pueden dar lugar a longitudes de llama más largas
- Las longitudes de llama más largas causan:
- Volcado de la llama para procesar los tubos
- Impacto de la llama en los tubos de proceso y puntos calientes
- Menor tiempo de funcionamiento entre las descoberturas
- Reducción de la producción de etileno
- ZeecoQuemador GLSF de llama plana y chorro mejorado montado en el suelo
- El quemador arrastra el combustible no quemado junto a la pared del horno
- Mezcla los productos inertes de la combustión con el gas combustible no quemado
- Resultados:
- Menor temperatura máxima de la llama
- Reducción de las emisiones de NOx
- Reducción de la tendencia al vuelco de la llama porque la mezcla se mantiene cerca de la pared del horno
Quemador de chorro plano mejorado GLSF
Los puertos escalonados en el lado del azulejo del quemador permiten:
- El gas combustible debe evitar pasar directamente sobre la corriente de aire de combustión
- Retraso en la mezcla de combustible y aire para reducir la temperatura máxima de la llama
- Reducción de la temperatura máxima de la llama para disminuir las emisiones de NOx
- Mayor impulso de combustible y aire en la pared del horno para reducir el potencial de vuelco de la llama
- Mejor control de la anchura y longitud de la llama
- Perfil de flujo térmico uniforme en las regiones media y superior de la llama del quemador
- Transferencia de calor uniforme y reducción de la posibilidad de puntos calientes en los tubos
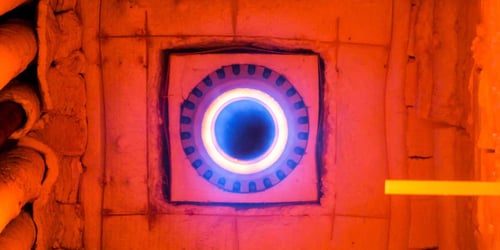
Conclusiones
- (8) nuevos hornos de craqueo de etileno necesarios para funcionar con menos de 90 mg/Nm3 de emisiones de NOx
- Después de la retroadaptación, los quemadores montados de cerca no mostraron signos de interacción de la llama ni de vuelco
- Los quemadores logran las emisiones deseadas, y normalmente funcionan muy por debajo de los niveles garantizados
- Las emisiones de NOx medidas en el campo fueron de 35 mg/Nm3 (17 ppmv) a 65 mg/Nm3 (32 ppmv) en la liberación de calor diseñada
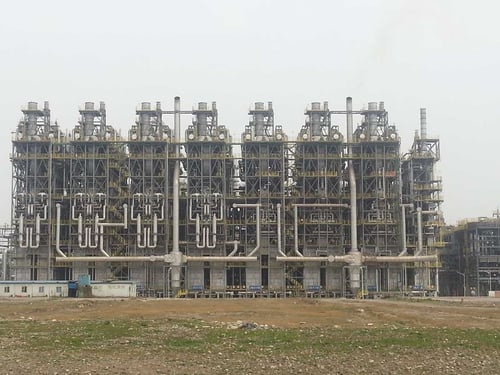
Descargar la presentación