Enfrentarse al rompecabezas de los azulejos
CATEGORÍAS:
David A. Short, Zeeco, Reino Unido, describe cómo se ha conseguido mejorar el diseño del tradicional azulejo para quemadores de pared radiante utilizado en los quemadores de proceso.
Las baldosas de los quemadores de pared radiante desempeñan un papel intrínseco en el mantenimiento de la temperatura del horno y de la estabilidad y eficacia del funcionamiento. Históricamente, los azulejos de los quemadores de pared radiante se fabricaban en cuatro piezas utilizando arcillas de ladrillo refractario cocidas al horno y moldeadas a mano, apoyadas en tacos de fijación laterales externos. Durante la década de 1970, la mayoría de las baldosas para quemadores de pared radiante se fabricaban en dos piezas utilizando material convencional de sílice fundida. Un sistema de retención de fijaciones laterales e inferiores se soldaba a la placa de montaje frontal del quemador (Figura 1). Este diseño fue adoptado por los principales fabricantes de quemadores de proceso y, en la mayoría de los casos, se sigue aplicando en la actualidad.
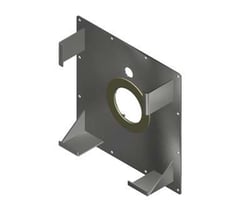
.
Sin embargo, este diseño no está exento de problemas. Los principales son el peso de la baldosa y los fallos del sistema de retención. Incluso cuando se funde en dos secciones, el denso material refractario es pesado y engorroso de instalar, y requiere un amplio sistema de anclaje y soporte, como se ve en la figura 1. El sistema de retención tradicional a menudo permite que el gas caliente penetre alrededor de la brecha de expansión de la teja del quemador y, debido a la contracción del refractario adyacente o al movimiento del mismo, el gas de recirculación/escape no sólo reduce la eficiencia y la estabilidad del horno, sino que aumenta la probabilidad de un fallo prematuro de las calas por el posible sobrecalentamiento de la placa de montaje del quemador o de la carcasa del horno.
Para garantizar que una baldosa tenga el rendimiento esperado, los usuarios finales deben tener en cuenta los criterios críticos de selección del material refractario. Entre ellos se encuentran:
- Temperatura de funcionamiento del horno
- Temperatura de la cara fría del horno
- Gas o aceite de combustión
- Atmósfera oxidante o reductora y composición de los gases
- Quemadores montados en el techo, en la pared o en el suelo
- Probabilidad de erosión por gas y/o ataque químico
- Probabilidad de impacto directo de la llama
- Condiciones del ciclo térmico.
Un nuevo diseño de baldosa modular
Los ingenieros de Zeeco se propusieron crear una baldosa con mayor integridad y fiabilidad. El diseño resultante, denominado Zeecolite, es una baldosa compuesta de una sola pieza para quemadores de pared radiantes (Figuras 2 y 3). Los componentes clave de este diseño incluyen una cara caliente resistente a la erosión y un aislamiento de apoyo de material térmicamente eficiente y ligero con anclaje seguro de acero inoxidable Inconel.
Figura 2. Baldosa de quemador de pared radiante de una pieza de Zeecolite - cara caliente.
Figura 3. Baldosa de quemador de pared radiante de una pieza de Zeecolite - cara fría.
El diseño modular de una sola pieza utiliza un molde de bajo contenido en cemento del 62% de alúmina y óxido férrico de 1700˚C especialmente formulado como cara caliente, respaldado por placas de aislamiento de fibra cerámica (Figura 4). El diseño proporciona tanto eficiencia térmica como resistencia a la erosión, criterios fundamentales para el rendimiento del quemador y la fiabilidad del hogar.
Figura 4. Vista lateral del diseño de las baldosas modulares mostrando las placas aislantes de fibra cerámica y el sistema de anclaje empotrado.
El conjunto de baldosas es autoportante con un sistema de anclaje empotrado de acero inoxidable de cuatro puntos. El sistema empotrado, totalmente cerrado, se utiliza para fijar el módulo de tejas a la carcasa del horno o a la placa de montaje del quemador. El sistema de anclaje es completamente independiente del refractario circundante del horno y de los componentes de combustión del sistema del quemador. La incrustación de los anclajes en la sección de fundición evita los problemas asociados a la fatiga y la oxidación del metal (figura 5).
Figura 5. Vista lateral del diseño de la baldosa modular que muestra los cáncamos acoplados para maniobrar la baldosa en su lugar.
Detrás de la cara caliente, la placa aislante de fibra cerámica proporciona la eficiencia térmica y reduce el peso. El módulo de tejas resultante con sistema de anclaje proporciona una mayor eficiencia térmica y un menor peso, necesidades fundamentales en los hornos modernos de hoy en día.
Cómo abordar los problemas de longevidad y puesta en marcha
Las baldosas de Zeecolite se secan previamente a 360˚C para garantizar la eliminación del agua libre y química. Este proceso anula el problema habitual de agrietamiento térmico o fallo de las baldosas durante los procedimientos de puesta en marcha. El sistema de anclaje totalmente protegido garantiza la integridad a largo plazo del sistema de soporte y evita cualquier movimiento hacia delante de la baldosa en relación con la punta del gas del quemador, lo que supone un reto de longevidad y fiabilidad común a los diseños tradicionales de baldosas. La adición del aislamiento de fibra cerámica de baja masa mejora la eficiencia térmica, lo que también reduce los costes relacionados con la energía para mantener el funcionamiento del horno dentro de las especificaciones de diseño y los objetivos de eficiencia.
Aplicaciones
La teja modular de una sola pieza ha sido diseñada para su uso en aplicaciones de quemadores de llama plana de combustión lateral en hornos de reformado primario. Tanto la sección de fundición de la cara caliente como el grosor de la placa aislante de fibra cerámica pueden variar en función del parámetro particular del horno o de la aplicación; este diseño es adecuado para cualquier construcción existente o nueva, independientemente del grosor de la pared o de la composición del refractario circundante.
Instalación
El módulo de baldosas del quemador está diseñado para que sea fácil de instalar tanto en aplicaciones nuevas como en las de reequipamiento. Los anclajes de acero inoxidable empotrados sobresalen a través de las placas aislantes de fibra cerámica posteriores para atornillarlas a la placa de montaje exterior. Para elevar primero los módulos hasta la ubicación de montaje en la pared del horno, se suministran normalmente cáncamos que se enroscan en los pernos de anclaje con los conjuntos de tejas. Una vez colocado, el sistema de montaje garantiza que los anclajes sean capaces de suspender el módulo de tejas del quemador sin ningún movimiento debido a la torsión gravitacional, lo que significa que el módulo de tejas no impartirá ninguna carga o tensión significativa al sistema de revestimiento circundante. Esta es una ventaja especial cuando se utilizan materiales delicados para el sistema de revestimiento, como los módulos de fibra cerámica refractaria (RCF). El montaje del módulo cerámico puede realizarse de forma interna o externa, dependiendo de si el módulo se fija a su vez a una placa de montaje del quemador o directamente a la carcasa del horno.
Si el patrón de los pernos de anclaje no coincide con la disposición existente en la placa de montaje del horno, se pueden taladrar agujeros adicionales en la placa de montaje utilizando un tablero de plantillas para ubicar los agujeros o, alternativamente, el módulo puede ser premontado en una nueva placa de montaje del quemador. Este tipo de módulo de azulejos se utiliza en muchos hornos de reformado de vapor y ha proporcionado ventajas de eficiencia térmica y longevidad.
Estudio de caso: Alemania
Un horno con quemadores de tiro natural de tiro lateral tenía un espesor de pared refractaria de 325 mm a través de la teja del quemador.
La baldosa original tenía una cara caliente de 250 mm de espesor y utilizaba un molde de silicato de alúmina de 1650˚C, con dos capas de fibra cerámica y placas de silicato de calcio que añadían otros 75 mm de espesor. La temperatura de la cara caliente podía alcanzar los 1200˚C, aunque a efectos de comparación del diseño de las baldosas, la temperatura media del hogar utilizada fue de 1100˚C. La temperatura de la cara fría, en condiciones ambientales de 21˚C y sin viento, era de 96˚C con una pérdida de calor de 936 W/m2.
El material de la cara caliente de la nueva baldosa estaba compuesto por un 62% de alúmina 1700˚C de bajo contenido en cemento y tenía un grosor de 60 mm entre los alambres de anclaje y de 160 mm a través de los alambres de anclaje, respaldado por 165 mm de placas aislantes de fibra cerámica. El espesor total del módulo era de 325 mm.
La media de la temperatura de la cara fría de las secciones moldeables, con las mismas condiciones ambientales, fue de 60˚C con una pérdida de calor media de 410 W/m2.
Como resultado de la aplicación de la nueva teja, se produjo una mejora del 56% en la eficiencia térmica con una reducción del peso del módulo de 79 kg/teja.
Estudio de caso: Austria
Un horno con quemadores de tiro natural de tiro lateral tenía un espesor de pared refractaria de 293 mm a través de la teja del quemador. La temperatura de la cara caliente podía alcanzar los 1200˚C, pero a efectos de comparación del diseño de las baldosas, la temperatura media de la cámara de combustión utilizada fue de 1100˚C.
La baldosa original tenía una cara caliente de 158 mm y utilizaba un molde de silicato de alúmina de 1650˚C, respaldado por tres capas de fibra cerámica y placas de silicato de calcio, que sumaban 135 mm. La temperatura de la cara fría, con condiciones ambientales de 21˚C y sin viento, era de 77˚C con una pérdida de calor de 645 W/m2.
El material de la cara caliente de la nueva teja estaba compuesto por un molde de bajo cemento con un 62% de alúmina de 1700˚C y tenía un grosor de 58 mm entre las bandas de anclaje y de 158 mm a través de las bandas de anclaje, con un respaldo de 135 mm de placas aislantes de fibra cerámica. La temperatura media de la cara fría de las dos secciones de hormigón, en las mismas condiciones ambientales, fue de 65˚C con una pérdida de calor media de 468 W/m2.
En consecuencia, se logró una mejora del 28% en la eficiencia térmica con una reducción del peso del módulo de 38 kg/tejido.
Conclusión
El nuevo diseño de las baldosas ha reducido el tiempo de inactividad del horno y ha mejorado la longevidad del producto. Además, si se une a la mejora de la eficiencia térmica, su aplicación ha supuesto un notable ahorro en los presupuestos de explotación y mantenimiento.
Figura 6. Funcionamiento de los quemadores murales radiantes en el horno con teja Zeecolite.
Descargar el artículo