Sustitución de quemadores de conducto en centrales de ciclo combinado
CATEGORÍAS:
Sustitución de quemadores de conducto en centrales de ciclo combinado
Muchas centrales eléctricas de ciclo combinado (CCPP) y plantas de cogeneración o de producción combinada de calor y electricidad (CHP) utilizan sistemas de encendido suplementarios, o quemadores de conducto, dentro de las calderas del generador de vapor con recuperación de calor (HRSG). Los quemadores de conducto pueden activarse a demanda para aumentar de forma rápida y eficiente la producción de vapor del HRSG al generador de turbina de vapor para añadir megavatios en las CCPP, donde la producción de megavatios puede ser a demanda o planificada previamente a partir del despacho aplicable del productor para apoyar la demanda de electricidad. Los quemadores de conducto también pueden aumentar la producción de vapor para uso de los clientes y, en última instancia, aumentar las ventas del productor de cogeneración.
En el mercado nacional, muchos quemadores de conductos se instalaron en CCPP y cogeneraciones/CHP nuevas construidas entre 1995 y 2005. Las instalaciones de quemadores de conductos se ralentizaron en CCPP y cogen/CHP nuevas entre 2005 y 2015. Desde 2015, la construcción de nuevas CCPP y cogeneración/CHP casi se ha paralizado debido a la economía y a la reciente presión de los organismos gubernamentales para investigar e invertir en tecnologías de combustibles ecológicos. Como resultado, la infraestructura de las centrales eléctricas en todo el mercado nacional está envejeciendo y necesita atención.
Lamentablemente, debido al envejecimiento de la infraestructura de los equipos existentes, muchos sistemas de quemadores de conductos que se utilizan hoy en día han alcanzado o se están acercando rápidamente al final de su ciclo de vida útil y presentan una serie de problemas para el productor, tales como:
- Aumento de los costes de mantenimiento para reparar continuamente los equipos
- Aumento de los costes operativos con mayores emisiones o impacto de llama en el HRSG
- Avería parcial de los quemadores, lo que crea problemas de apagado y fiabilidad.
- Avería total de los quemadores, lo que provoca problemas tan simples como que los quemadores dejen de funcionar y tan complejos como que los quemadores se desplomen sobre el suelo del HRSG.
- Deterioro continuado de los equipos antiguos a un ritmo exponencial en el tiempo
Las inspecciones documentadas frecuentes y el control de supervisión de los equipos antiguos son vitales para comprender el estado actual de los quemadores de conductos de una instalación y saber cuándo se deben presupuestar los costes de capital para reparaciones o sustituciones. Las inspecciones pueden realizarse mientras el equipo está en funcionamiento, pero es mejor realizarlas durante las paradas, normalmente en primavera y otoño, y deben ser realizadas por una empresa de combustión acreditada. Estas inspecciones pueden identificar problemas que pueden afectar a los equipos existentes, diagnosticar por qué se han producido fallos y determinar si la sustitución es más económica que el mantenimiento continuado. Las inspecciones pueden completarse en tan sólo un día si se coordinan adecuadamente para no retrasar el reinicio de la instalación.
La sustitución de los sistemas de quemadores de conductos suele ser más fácil de lo que la mayoría de los productores creen. Este puede ser el mejor enfoque para preservar el ciclo de vida de las capacidades de producción de energía porque la sustitución detiene el proceso de envejecimiento y reinicia el reloj para el productor, eliminando una de las muchas preocupaciones para el equipo de gestión. Este estudio de un caso de sustitución llave en mano de un sistema de quemadores de conductos (figura 1) realizado por Zeeco ayuda a los propietarios de instalaciones a comprender el camino desde el diagnóstico hasta la puesta en marcha y demuestra las ventajas de eliminar los equipos obsoletos de la infraestructura de una central eléctrica.
La situación
En 2022, una importante empresa de suministro eléctrico del sureste de EE.UU. se puso en contacto con Zeeco para plantear sus dudas sobre el sistema de quemadores de conductos existente. Zeeco realizó una inspección de la instalación y registró los resultados, entre los que se incluían:
- Estabilizadores de llama en mal estado
- Fallo del piloto de la llama de combustible principal del elemento quemador
- Reconocimiento deficiente del escáner de llama
- Impacto de la llama en la sección tubular del HRSG aguas abajo
Los estabilizadores de llama deformados y distorsionados pueden ser el resultado de la incapacidad de controlar la forma de la llama debido a un flujo deficiente de los gases de escape de la turbina (TEG). Esto suele deberse a diseños antiguos que siempre fueron inadecuados pero desconocidos hasta la introducción de nuevas tecnologías. El simple proceso de envejecimiento de los equipos de combustión sometidos a años de ciclos de encendido y apagado también desgasta los soportes de llama y los cuerpos de los faros. En este caso, se observó que ambos contribuían al deterioro del equipo.
La incapacidad del piloto para encender las llamas del combustible principal puede deberse al hundimiento de los elementos del quemador. Otras causas de este fallo son simplemente la destrucción del dispositivo o dispositivos de chispas que residen dentro del entorno del horno HRSG día tras día a temperaturas extremas. El circuito eléctrico general de los sistemas de encendido de alta energía se ve fácilmente perturbado por el vapor de agua del TEG y los sistemas de conductos abiertos, que a menudo pueden estar empapados de agua de lluvia. En este caso, el hundimiento del elemento del quemador fue la causa principal de que el piloto no encendiera el combustible principal. Las puntas de las chispas ya no estaban en la trayectoria del combustible principal y nunca tuvieron la oportunidad de encenderse.
El reconocimiento deficiente de la llama principal del combustible por parte del detector de llama también puede atribuirse a varias cuestiones:
- Elementos del quemador combados.
- Suciedad, residuos o vapor de agua cubriendo la lente del guardallamas.
- Movimiento involuntario del sistema de montaje del guardallamas debido a las fuertes vibraciones normales del HRSG.
- Modelos de escáner antiguos que utilizan algoritmos de reconocimiento de llama obsoletos que no pueden distinguir correctamente entre llama y ausencia de llama.
Los componentes electrónicos no duran eternamente y pueden provocar fácilmente un reconocimiento deficiente de la llama.
En este caso, los escáneres eran de tecnología antigua y se habían desgastado en varias fases a lo largo de las múltiples elevaciones del quemador.
El impacto de la llama en la sección de tubos HRSG aguas abajo es el principal destructor de las calderas HRSG, y la reparación de esos largos tubos de caldera de aleación cuesta millones. Las llamas largas y perezosas crean el impacto de la llama cuando el sistema del quemador introduce el combustible crudo en el horno de la HRSG (bajo el control total del sistema de gestión del quemador [BMS]) y es encendido por el encendedor piloto. Una vez que la llama del combustible principal está encendida y es reconocida por el escáner de llama, el sistema de control distribuido (DCS) del HRSG permite aumentar el combustible para satisfacer la demanda de vapor de salida.
Sin embargo, a medida que las puntas del quemador se erosionan bajo la presión del combustible con el paso del tiempo, o los estabilizadores de llama se deforman debido a la recirculación del flujo de TEG y la llama del quemador, o a medida que los elementos del quemador se hunden (Figura 2), se permite que el combustible fluya más aguas abajo de la punta del quemador antes de que se produzca la combustión real o completa. Estos factores pueden permitir que las llamas crezcan más hasta que impacten en los tubos. Con el tiempo, el impacto destruirá los tubos. Este problema debe corregirse, o el fallo futuro es inminente. En este caso, las llamas más largas causadas por las puntas erosionadas del quemador contribuyeron al impacto de la llama.
El desafío
Este proyecto incluía retos tanto comunes como específicos de cada situación. En concreto, la parada planificada con antelación estaba programada para 18 días en primavera y se clasificó como parada no importante, lo que significa que no estaba previsto realizar modificaciones en la turbina de combustión ni en la turbina de vapor durante esta parada. Las paradas suelen planificarse con mucha antelación en muchos emplazamientos, por lo que es muy importante conocer el estado actual de los equipos de quemadores de conductos para poder sustituirlos sin interrumpir o alterar los programas de paradas planificados previamente.
El cliente explicó además que esta instalación era crítica para la red en el sentido de que la demanda de producción de vapor y de megavatios era de la máxima importancia debido a la enorme base de clientes. No se podía dejar pasar la interrupción, y la unidad tenía que estar operativa el último día de la interrupción. La siguiente interrupción prevista para este emplazamiento no se produciría hasta dentro de varios años, lo que añadía otra consideración importante a los equipos y la instalación. Fue necesaria una planificación exhaustiva "llave en mano" para superar este reto de calendario, y la comunicación constante con la instalación fue fundamental.
Por lo general, el diseño y la instalación deben ajustarse al valor de coste del presupuesto de capital preaprobado para la parada. En este caso, el cliente tenía un presupuesto de capital aprobado aproximadamente dos años antes de la compra de los nuevos quemadores. Sin embargo, la inflación dentro de la economía y la pandemia de re-cent hicieron que el precio de los materiales fuera una preocupación imprevista.
La sincronización de la solicitud de presupuesto con las fechas de interrupción de la instalación fue clave para el éxito. El diseño, la fabricación, la entrega y la instalación consumen varias semanas del programa general para poder llevarse a cabo con éxito. Por lo tanto, era crucial encargar los equipos mucho antes de la fecha prevista para la parada. Una vez más, conocer el estado actual del equipo de quemadores de conductos permitió al propietario de la instalación planificar la sustitución adecuadamente.
Proceso del proyecto
El diseño de la reconversión corrió a cargo de un equipo altamente experimentado que ha realizado con éxito numerosos proyectos llave en mano de sustitución de quemadores de conductos, así como diseños y fabricación de quemadores de conductos totalmente nuevos para una amplia lista de fabricantes de equipos originales de todo el mundo. Mantener un solo equipo de ingenieros y gestores en el proyecto refuerza las relaciones con el equipo del cliente y elimina las lagunas de información en todo el proyecto.
Las compras de material fueron realizadas por personal con amplia formación en la búsqueda de los mejores precios y entregas. Zeeco utiliza una extensa lista de fabricantes homologados supervisada por su programa de la Organización Internacional de Normalización (ISO), lo que da un enorme poder adquisitivo a los compradores implicados y elimina la necesidad de preocuparse por proveedores nuevos o no probados.
La fabricación de los equipos en una de las siete plantas de producción mundiales de Zeecofue supervisada de cerca por el equipo de Garantía de Calidad/Control de Calidad (QA/QC) y el equipo de ingeniería de ejecución del proyecto. La entrega fue planificada y realizada por un equipo logístico de expertos en transporte. Antes de la fase de ejecución del proyecto, Zeeco creó un esquema y un plan muy específicos, tarea por tarea, para todos los trabajos mecánicos y eléctricos que debían realizarse in situ. El plan aplicado fue seguido por experimentados equipos de construcción.
Descubrimiento
Casi todos los proyectos de instalación llave en mano producen algún descubrimiento que identifica problemas desconocidos antes del inicio de la demolición del equipo existente. En el caso de este proyecto, el descubrimiento fue una corrosión interna grave en las paredes de la carcasa de acero al carbono del HRSG (figura 3). Este tipo de descubrimiento es cada vez más común en equipos antiguos de HRSG y quemadores de conductos, especialmente cuando las unidades de HRSG se instalan originalmente cerca de entornos marinos o en lugares donde las temperaturas extremas pueden hacer que la carcasa expuesta, el aislamiento de la pared cerrada del HRSG y el sistema de placa de revestimiento flotante interno del HRSG trabajen con extraordinaria dureza.
Otros descubrimientos habituales en este tipo de HRSG y quemadores de conducto son la corrosión interna de las tuberías de combustible, la reducción del grosor de las paredes de las tuberías de presión y la corrosión o destrucción de los asientos de las válvulas. Estos problemas se desarrollan con el tiempo debido a las fluctuaciones de temperatura del combustible a lo largo de la infraestructura de tuberías de combustible de la planta causadas por los cambios climáticos y las condiciones estacionales. Para este proyecto ya estaba prevista la sustitución de las tuberías externas por tuberías, accesorios y válvulas nuevos sin corrosión.
La solución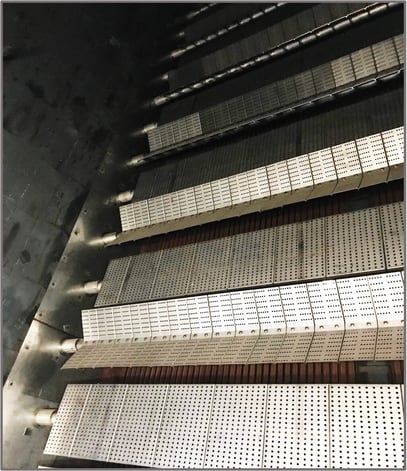
Este proyecto llave en mano de sustitución de quemadores de conductos se planificó teniendo en cuenta esos tipos habituales de descubrimientos. Cada posible descubrimiento se discute con el cliente antes de finalizar la compra del equipo y la instalación llave en mano. La mitigación de los descubrimientos por adelantado a través de una planificación detallada crea un programa de rendimiento que es lo más exacto posible a los escenarios del mundo real y ayuda a eliminar las sorpresas.
Durante una parada programada, es frecuente que otros contratistas trabajen en otros equipos, como las torres de refrigeración o las cubas y válvulas de alivio de los tambores de las calderas. El lugar puede congestionarse, y los remolques de herramientas y las oficinas de construcción pueden reducir las zonas de almacenamiento de material. Si se recurre a una empresa de instalación reputada y se garantiza la asistencia diaria a las reuniones de interrupción, todos los contratistas podrán expresar y compartir a diario sus preocupaciones y planes prospectivos. La coordinación entre los contratistas puede evitar problemas como la competencia por una grúa o espacios de grúas de techo y espacios libres para pruebas radiográficas de exámenes no destructivos, así como la congestión de las carreteras debido a la entrega de materiales y consumibles. Un proyecto bien comunicado es un proyecto más seguro, que elimina accidentes y puede salvar vidas.
Resultados y beneficios
Tras la puesta en marcha de este proyecto y la desmovilización del equipo de instalación, los beneficios para este cliente fueron muy claros. Cada uno de los puntos siguientes satisfizo las necesidades del cliente y devolvió al sistema de quemadores de conductos la vida que necesitaba durante muchos años.
Éxito llave en mano
La sustitución del quemador del conducto se llevó a cabo en 16 días en lugar de los 18 previstos, lo que permitió volver a encender la unidad el último día de la parada.
Coste
En este caso, el poder de compra global de Zeecopermitió al equipo abastecerse de materiales y ahorrarse el valor del presupuesto de capital original creado con mucha antelación a la compra del equipo.
Equipos nuevos
El cliente dispone ahora de un nuevo sistema de quemadores de conductos sin ninguno de los problemas anteriores. El ahorro económico derivado de la reducción de los costes de mantenimiento y funcionamiento se traducirá en un ahorro a lo largo del tiempo.
Equipamiento correcto
El diseño y la instalación se ajustaron al 100% al pliego de condiciones, por lo que el cliente recibió todo lo que pedía en una sola interrupción y con un coste presupuestario.
Liberación de calor
El nuevo equipo suministra la cantidad adecuada de calor a la caldera HRSG para una producción óptima de vapor.
Fabricación
Zeeco utilizó una de las siete plantas de fabricación propias en todo el mundo para completar el equipo a tiempo y cumpliendo plenamente los requisitos de aseguramiento de la calidad y control de calidad tanto internos de la empresa como del cliente.
Entrega
Saber que los equipos adquiridos se entregarían en el emplazamiento utilizando el sistema logístico del proveedor ahorró muchas horas de supervisión y preocupación a la dirección del cliente.
Instalación
Esta instalación llave en mano utilizó uno de los muchos equipos de instalación mecánica y eléctrica que Zeeco utiliza y gestiona. Una instalación llave en mano completa también ahorró al cliente muchas horas de supervisión y preocupación por parte de la dirección.
Puntualidad
El proyecto se terminó antes de lo previsto y con el coste presupuestado, lo que benefició al productor y garantizó que la interrupción prevista fuera correcta y no fuera necesaria ninguna prórroga.
Cero incidentes o accidentes de seguridad
Al final de cada jornada, todo el mundo volvía a casa sin lesiones. A largo plazo, las primas de seguro siguen siendo bajas, los indicadores de seguimiento de la seguridad de las instalaciones se mantienen intachables y el historial de seguridad de la empresa permanece intachable.
Acceso mejorado
Las zonas de acceso menos congestionadas en la parte frontal del quemador permiten un mejor mantenimiento y funcionamiento, al tiempo que crean entornos de trabajo más seguros.
Entrenamiento
Formar al equipo de operaciones en los nuevos equipos del proveedor es vital para lograr un funcionamiento impecable y reducir los desplazamientos innecesarios.
Emisiones
Contar con nueva tecnología de equipos reduce enormemente las emisiones en muchos casos y permite a las empresas operadoras mantenerse dentro de sus tolerancias de emisiones.
Protección de equipos
La forma de la llama bien anclada y las longitudes de la llama que se ajustan bien dentro del horno HRSG eliminan los daños en las secciones de tubo aguas abajo, las paredes del revestimiento, los techos y el suelo.
Cumplimiento de la Asociación Nacional de Protección contra Incendios (NFPA)
La norma NFPA 85, que rige los quemadores de conductos, y concretamente el capítulo 8, se actualiza con frecuencia. Disponer de un equipo nuevo significa que las salvaguardias reguladoras ya están en vigor.
Garantía
Los equipos nuevos ofrecen garantías limitadas a los propietarios de las instalaciones.