Una solución rentable para el cumplimiento de las normas de emisión
CATEGORÍAS:
Los elevados costes de capital suponen un reto importante para los operadores de almacenamiento a la hora de garantizar que sus unidades de recuperación de vapores más antiguas cumplan con la normativa sobre emisiones. Una renovación de la unidad de recuperación de vapores es una solución rentable para garantizar que la unidad cumple con la normativa más reciente.
En todo el mundo, los sistemas de recuperación de vapores son habituales en las refinerías, las terminales de distribución y las instalaciones de almacenamiento en tanques, donde se transfieren productos que van desde la gasolina hasta los aromáticos, como el benceno y los xilenos, y, cada vez más, el petróleo crudo.
Cuando se transfieren hidrocarburos entre barcos, ferrocarriles, camiones cisterna y tanques de almacenamiento, una fracción del producto suele liberarse en forma de vapor. Aunque la fracción puede ser pequeña, la liberación acumulada puede ser sustancial debido a las grandes cantidades de producto -normalmente de 10.000m3 /h a 1.000m3 /h- y a los mayores flujos de vapor típicos de las aplicaciones de carga marítima. A menos que se utilice una tecnología de control de vapores, éstos se liberan a la atmósfera con un efecto perjudicial para el medio ambiente, la salud y las infraestructuras cercanas.
La recuperación de vapores de carbón activado (figura 1) sigue siendo la tecnología preferida en la mayoría de las aplicaciones, a menudo denominada la mejor tecnología disponible (MTD). Estos sistemas ofrecen a los operadores la máxima flexibilidad, ya que manejan una amplia gama de productos y cuentan con una amplia relación de reducción del 0% al 100% del flujo de diseño y de las concentraciones de entrada.
Figura 1. Una VRU húmeda típica con dos lechos de carbón, dos bombas de vacío de anillo líquido, un recipiente separador de glicol y una columna de absorción.
Los legisladores de todo el mundo exigen continuamente una mayor capacidad de control de las emisiones a los operadores y diseñadores de sistemas. Los requisitos actuales se fijan ahora en 50 mg (HC) / Nm3 para cualquier emisión media de una hora en algunas partes de Europa. Naturalmente, los proveedores de sistemas deben adaptarse y desarrollar diseños para cumplir estas nuevas normativas y exigencias. La legislación en materia de contaminación ambiental seguirá siendo siempre el motor del desarrollo de la tecnología de recuperación de vapores y de la inversión de capital de los operadores, debido a las importantes sanciones económicas que conlleva el incumplimiento de los requisitos en materia de emisiones. Pero en situaciones en las que una gran inversión de capital no es asequible, ¿qué opciones tienen los operadores a la hora de enfrentarse a una nueva normativa o a un aumento del rendimiento de las terminales?
Es imperativo que las unidades de recuperación de vapores estén correctamente dimensionadas para el flujo de vapor, la concentración de vapor y los objetivos de emisión deseados. Es posible que las unidades más antiguas no puedan seguir el ritmo ante el aumento de la producción o las nuevas normativas. Una solución es una nueva unidad de recuperación de vapores diseñada específicamente para reducir las emisiones y aumentar la capacidad; sin embargo, estas unidades tienen un alto coste de capital y largos plazos de entrega. Como alternativa, a menudo es posible modernizar, renovar y mejorar las unidades de recuperación de vapores existentes in situ, minimizando los costes de capital, los plazos de entrega y el tiempo de inactividad de la planta.
Las unidades de recuperación de vapores pueden ser revisadas y mejoradas de varias maneras, dependiendo de las necesidades del usuario final. Fundamentalmente, se requiere una mayor masa de carbón activado y un mayor caudal de vacío. Sin embargo, no siempre es posible añadir más carbón activado. Normalmente, los recipientes de carbón activado no tienen volumen libre disponible. En los casos en los que no es posible sustituir los recipientes de lecho de carbón por unidades más grandes, el tiempo en el que cada recipiente está en la fase de adsorción puede ajustarse, dentro de los límites de diseño, para garantizar que no se superen los límites de emisión cerca del final de cada ciclo.
En muchos casos resulta ventajoso sustituir las bombas de vacío de anillo líquido (LRVP) "húmedas" y los sistemas de fluido de sellado por una adaptación "seca". De este modo, se sustituye la LRVP (representada en la figura 3) por una bomba seca de tornillo o de paletas adaptada específicamente a las condiciones físicas presentes en el proceso y en el emplazamiento. Los sistemas "húmedos", que antes se consideraban una forma sólida de suministro de vacío, suelen requerir un mantenimiento más oneroso, ya que el fluido de sellado debe mantenerse en una composición constante para que funcione correctamente. Ahora, debido a los avances en el diseño y la capacidad, las bombas de vacío de sistemas secos son cada vez más versátiles, con la capacidad de funcionar de forma fiable en condiciones extremas y con temperaturas variables debido a la inyección de gasolina o al trazado de calor para la gestión de la temperatura. Un momento ideal para integrar estos sistemas adicionales es durante una renovación de la VRU. Otro motivo para que los operadores eliminen las LRVP y las sustituyan por bombas de tornillo es el creciente uso de gasolinas mezcladas con etanol. El fluido de sellado de las LRVP se contamina con etanol durante su uso y se diluye rápidamente hasta un nivel que reduce la capacidad efectiva de las bombas. Una bomba de tornillo seca no sufre estos problemas.
Figura 3. LRVP.
Cuando se ha aumentado la capacidad de la VRU, generalmente también se requiere aumentar la capacidad de la bomba de vacío, ya que los hidrocarburos adsorbidos ahora deben regenerarse en un período de tiempo más corto. Para una unidad de recuperación de vapores de bajas emisiones, la bomba de vacío debe ser capaz de alcanzar vacíos relativamente bajos; de 50 a 35 mbaras, al tiempo que regenera el lecho de carbón en un periodo mucho más corto. Esto puede lograrse sustituyendo el sistema de bomba de vacío existente por un sistema de mayor capacidad. El lado negativo de la reducción del tiempo de adsorción es que la vida útil del carbón se reduce como resultado de más ciclos de regeneración en un tiempo determinado.
Los aumentos en la capacidad de vacío inician cambios en el equipo subsiguiente dentro de la unidad de recuperación de vapores en línea descendente desde la bomba de vacío. Por ejemplo, en las unidades de recuperación de vapores que cuentan con una bomba de vacío de anillo líquido, el separador de glicol (Figura 4) también tendría que ser mejorado con un recipiente más grande para acomodar la mayor capacidad de flujo requerida por una bomba de vacío de anillo líquido de mayor capacidad, que ha sido redimensionada para acomodar el mayor flujo de vapor.
Figura 4. Un separador de glicol.
También puede ser necesario sustituir la torre de absorción para adaptarla a mayores capacidades de la bomba de vacío o a cambios en las propiedades del absorbente: temperatura y presión de vapor. La eficiencia de la absorción está directamente relacionada con las características físicas del absorbente (temperatura y presión de vapor), el flujo de absorbente y gas (vapor), y el diámetro y la altura del absorbedor, todo lo cual tendrá que ser revisado y potencialmente aumentado cuando se instale una bomba de vacío más grande.
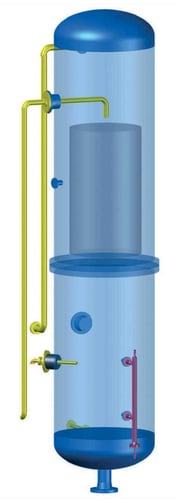
Una sustitución completa de la torre de absorción es costosa; las opciones alternativas pueden incluir la adición de una válvula de control de la presión en la línea de reciclaje desde la columna de absorción hasta los lechos de carbono. Esta válvula puede ser dimensionada para mantener una presión de funcionamiento dentro de la torre de absorción para mejorar el rendimiento del proceso. También hay que tener en cuenta factores secundarios, como el aumento de las temperaturas en la descarga de la bomba de vacío, que puede requerir posteriormente una refrigeración adicional, quizá en forma de inyección de gasolina o, en el caso de un sistema húmedo, un aumento del tamaño del intercambiador de calor instalado.
Además de aumentar la capacidad y reducir las emisiones de hidrocarburos, las renovaciones de las unidades de recuperación de vapores también pueden ofrecer un mayor control, características, versatilidad y seguridad para el usuario final. Esto puede lograrse mediante la adición de bombas de vacío adicionales para la redundancia; nuevas actualizaciones de CIM/CEM y analizadores para el control preciso de las emisiones; válvulas y actuadores mejorados; y transmisores de temperatura, presión y nivel. Los nuevos equipos pueden integrarse perfectamente con un sistema PLC/HMI actualizado, junto con una teoría de control a medida, para reducir las posibilidades de que se produzca un incidente de altas emisiones. Una ventaja adicional de la sustitución de los equipos existentes es que se elimina el problema del legado de los equipos que ya no cuentan con el apoyo del OEM, especialmente en lo que respecta a los sistemas PLC/HMI.
Figura 6. Modificaciones en el patín de la tubería.
El mantenimiento de la VRU renovada es tan importante como la selección del proveedor adecuado y la ingeniería posterior realizada durante la renovación. El carbón activado de las VRU de bajas emisiones está sometido a una mayor fuerza mecánica y, en algunos casos, a productos químicos no deseados, que impiden la adsorción. Por lo tanto, es imperativo respetar los intervalos de servicio recomendados y probar el carbón activado periódicamente, mitigando así el riesgo de daños continuos que, de otro modo, conducirían a un fallo repentino.
Una renovación de la unidad de recuperación de vapores es un compromiso sólido para los operadores que buscan aumentar la capacidad de la terminal sin dejar de cumplir con las emisiones, o para los operadores que buscan cumplir con la nueva normativa de emisiones de HC sin el desembolso de capital de una nueva VRU. A pesar de la amplia sustitución de equipos necesaria, una renovación de la unidad de recuperación de vapores sigue siendo una solución más rentable que la instalación de una unidad nueva en muchos casos.
Para renovar con éxito una VRU se requiere una experiencia significativa, como la de Zeeco, con una amplia variedad de sistemas VRU debido a las complejas interacciones de los equipos en todo el sistema. Zeeco también puede ofrecer servicio en equipos que no fueron suministrados originalmente por ellos.
Para más información
Este artículo ha sido escrito por Tom Olver, ingeniero técnico de ventas, proyectos y puesta en marcha de Zeeco Europe.
Descargar el artículo