Residuos que contienen nitrógeno: Oxidantes térmicos
CATEGORÍAS:
Zeeco es el líder mundial en soluciones de combustión con muy bajo NOx. Durante décadas, nuestros ingenieros han diseñado a medida oxidadores térmicos de residuos que contienen nitrógeno para plantas petroquímicas, refinerías de petróleo, fabricantes de fibra de carbono y empresas electrónicas. En este mismo momento, nuestros sistemas de combustión están eliminando residuos peligrosos y minimizando las emisiones medioambientales en todos los rincones del planeta.
Los incineradores térmicos de residuos ligados al nitrógeno son sistemas de incineración que tratan residuos gaseosos y líquidos compuestos por compuestos ligados al nitrógeno, como el amoniaco y el cianuro. La incineración a alta temperatura de residuos ligados al nitrógeno en un entorno oxidante (exceso de aire) produce niveles inaceptables de óxidos de nitrógeno (NOx).
Para limitar la formación de NOx, Zeeco emplea un proceso de incineración multietapa de bajo NOx. Nuestro diseño propio establece la norma para los sistemas de oxidación térmica de bajo NOx.
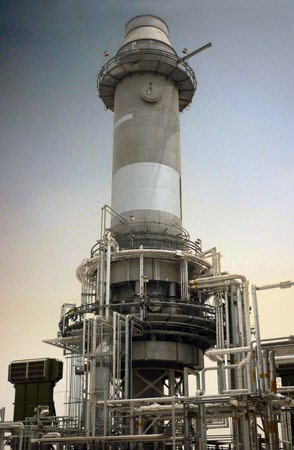
Requisitos más exigentes, soluciones duraderas.
Nuestro Centro de Investigación y Pruebas de Combustión está considerado uno de los mejores del planeta y fue el primero del mundo en obtener la certificación ISO 9001-2000. Nuestro personal se mantiene a la vanguardia de la rápida evolución de los requisitos medioambientales en materia de emisiones, al tiempo que supera las expectativas de nuestros clientes en cuanto a calidad y rendimiento duradero.
Con 15 hornos de pruebas de combustión a escala real, Zeeco es capaz de probar una amplia variedad de sistemas de combustión en condiciones de campo simuladas. Disponemos de múltiples combustibles líquidos y gaseosos que nos permiten simular prácticamente cualquier combustible especificado en condiciones de proceso específicas. Un sistema de incineración de varios flujos nos permite probar las situaciones más complejas en un entorno controlado. Zeeco también está equipado para realizar demostraciones de una amplia gama de equipos de quemadores y antorchas, incluidos quemadores de proceso, quemadores de caldera y todo tipo de equipos de antorcha, incluida una gran variedad de tecnologías sin humo.
Modelado computacional
Zeeco combina las capacidades avanzadas de la dinámica de fluidos computacional (CFD) con nuestra amplia experiencia en el diseño, la fabricación y el funcionamiento de equipos de combustión para garantizar un rendimiento óptimo. Al modelar las condiciones de proceso específicas de nuestros clientes en función del diseño real de los equipos, la CFD nos permite predecir lo que de otro modo no podríamos ver o prever, en lugar de basarnos únicamente en la experiencia pasada y en las reglas de diseño tradicionales.
Primera etapa: Horno de reducción
La primera etapa suele consistir en quemar los residuos y el combustible juntos en un entorno reductor (por ejemplo, con menos del requisito estequiométrico de oxígeno) a una temperatura controlada de 2000-2400°F (~1100-1300°C) o superior y un tiempo de permanencia de hasta 2,0 segundos. Este entorno de alta temperatura y los niveles subestequiométricos de oxígeno hacen que los compuestos que contienen nitrógeno ligado se disocien, produciendo finalmente nitrógeno libre. Debido al suministro de oxígeno subestequiométrico, en el efluente de la primera fase existen combustibles como el monóxido de carbono (CO2) y el hidrógeno (H2).
Segunda etapa: Quench
La segunda etapa enfría el efluente de la primera etapa a una temperatura inferior que oscila entre la temperatura umbral de formación de NOx y la temperatura de autoignición de los gases de combustión. El tiempo de permanencia en la segunda etapa suele oscilar entre 0,5 y 1,0 segundos. En esta zona se introduce un medio de refrigeración inerte, como agua, vapor o gases de combustión reciclados, para alcanzar estas temperaturas, que suelen oscilar entre 1300-1600°F (~700-870°C).
Tercera etapa: Horno de oxidación
La tercera etapa oxida los combustibles presentes en el efluente de la segunda etapa, ya templado. Los combustibles que se oxidan en la tercera etapa incluyen el CO2, el H2 y los hidrocarburos restantes que no pueden liberarse sin tratar a la atmósfera. Para completar el proceso de combustión, se introduce aire suplementario en los gases de combustión enfriados para que los combustibles restantes se oxiden antes de su descarga a la atmósfera. La temperatura de funcionamiento en esta etapa final suele limitarse a 1800°F (~980°C) y el tiempo de residencia en esta etapa final suele ser de 1,0-2,0 segundos.
Desempeño típico
- NOx emissions for Nitrogen Bound Waste Streams <100 ppm (vd)
- Eficiencia de destrucción de residuos (DRE) > 99,99% (disponible hasta el 99,9999%)
Aplicaciones típicas
- Aplicaciones petroquímicas con aminas, nitrilos, etc.
- Vapores de amoníaco y/o cianuro
- Unidades de recuperación de azufre: Extractor de agua ácida (SWS) Corrientes de gas por encima de la cabeza
- Fabricación de fibra de carbono LT/HT Flujos de gas no deseado
- Flujos de ventilación en la fabricación de productos electrónicos
Características de diseño propias:
- Rendimiento de emisiones predecible garantizado
- Reencendido correcto en la etapa de oxidación
- El aire de combustión del quemador se separa eficazmente del aire de combustión residual para un control óptimo
- Control del proceso y fiabilidad a largo plazo